Driving Innovation: Exploring the Role of Digital Twins in the Automobile Industry
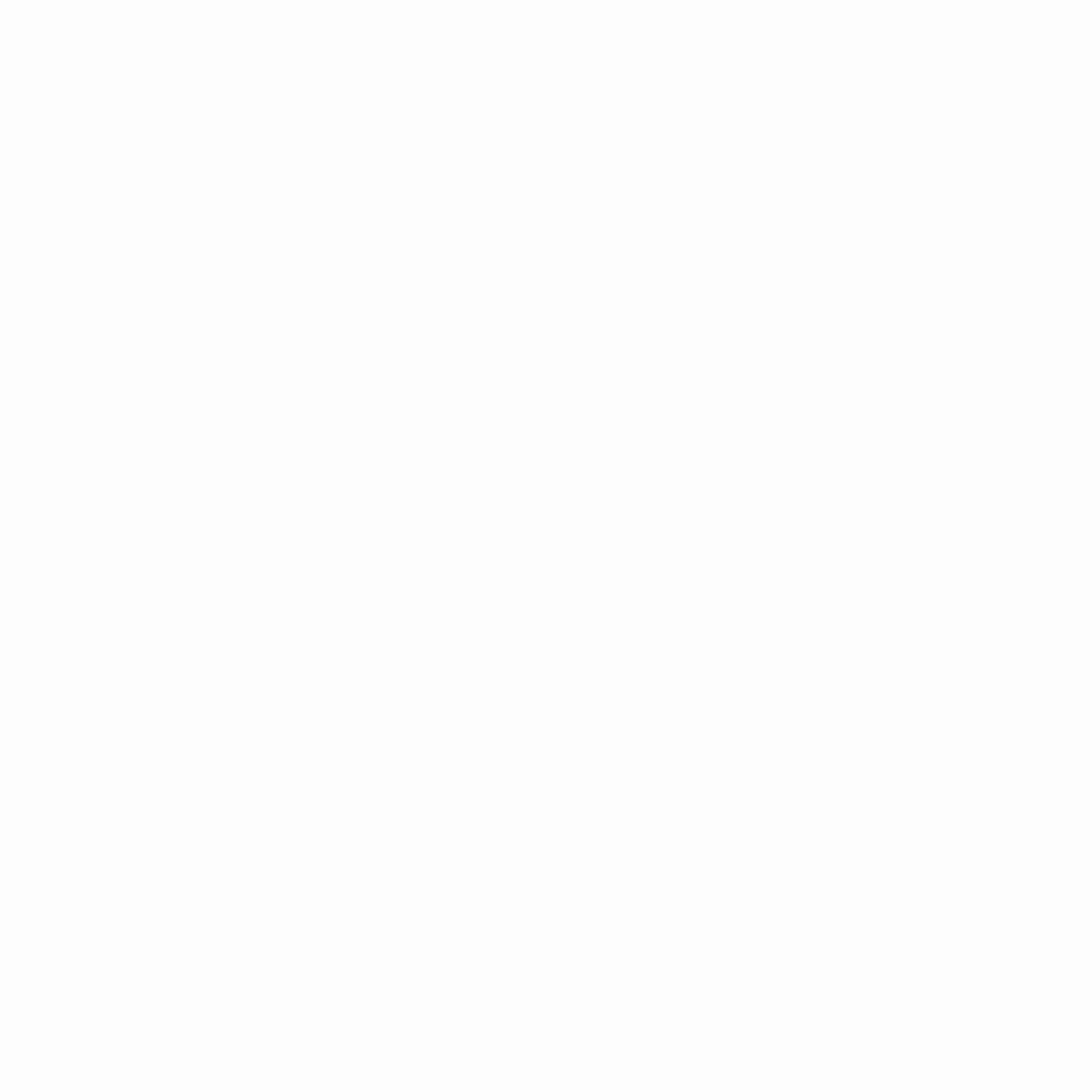
The automobile industry, a hub of technological advancement, is harnessing the power of Digital Twins to revolutionize design, manufacturing, and performance. These virtual replicas of vehicles and production processes offer a new dimension of insight and efficiency, enabling manufacturers to create cutting-edge vehicles while reducing costs and time-to-market. In this comprehensive article, we delve into the ways in which digital twins are shaping the automobile industry today, with real-world examples that illustrate their transformative impact.
Revolutionizing Vehicle Design
1. Conceptualization and Visualization
Digital Twins empower automobile manufacturers to conceptualize and visualize vehicles in a virtual environment. Designers can create 3D models of cars, experiment with different styles, and simulate real-world conditions to assess aesthetics and aerodynamics.
2. Iterative Prototyping*
Manufacturers can create virtual prototypes of vehicles, allowing for iterative design improvements. By simulating various parameters, such as weight distribution and wind resistance, manufacturers can refine designs before physical prototypes are produced.
3. Enhancing Collaboration*
Digital twins facilitate collaboration among design teams. Engineers, designers, and stakeholders can review, modify, and comment on virtual designs in real-time, streamlining communication and reducing design errors.
Example: A leading automobile manufacturer uses Digital twins to create virtual prototypes of upcoming vehicle models. By simulating factors like airflow, engine performance, and driver experience, the manufacturer can fine-tune designs before physical production begins.
Optimizing Manufacturing Processes
1. Assembly Line Simulation*
Digital twins allow manufacturers to simulate assembly line processes virtually. By replicating the production line, manufacturers can identify bottlenecks, optimize workflow, and minimize downtime.
2. Predictive Maintenance*
Integrating sensors into physical production processes, coupled with digital twins, enables predictive maintenance. Manufacturers can monitor equipment health in real-time, detecting potential issues and preventing unexpected downtime.
3. Quality Assurance*
Manufacturers can use digital twins to perform virtual quality checks on vehicles. By comparing the virtual model with real-time data from production, manufacturers can identify defects early in the process.
Example: An automobile assembly plant employs digital twins to simulate the entire production process. This allows them to identify potential collision points, optimize robotic movements, and reduce the risk of errors on the assembly line.
Enhancing Vehicle Performance and Testing
1. Performance Simulation*
Digital twins enable manufacturers to simulate vehicle performance in diverse conditions. Engineers can test factors like acceleration, braking, and handling virtually, ensuring optimal performance on the road.
2. Fuel Efficiency and Emissions*
By incorporating real-world data and virtual simulations, manufacturers can optimize fuel efficiency and reduce emissions. Digital twins help engineers identify areas for improvement without relying solely on physical testing.
3. Safety Testing*
Digital twins facilitate virtual safety testing. Manufacturers can simulate crash scenarios, analyze impact points, and assess safety features without the need for physical crash tests.
Example: An automotive company leverages digital twins to simulate vehicle performance in different climate conditions. By virtually testing the impact of extreme temperatures on battery life, engine performance, and cabin comfort, they can optimize vehicle systems for various environments.
Shaping the Future of Mobility
1. Autonomous Vehicle Development*
Digital twins play a crucial role in developing autonomous vehicles. Manufacturers can simulate driving scenarios, train AI algorithms, and validate safety systems in a virtual environment before testing on real roads.
2. User Experience Enhancement*
Manufacturers use digital twins to optimize the in-car user experience. They simulate the user interface, test connectivity features, and ensure that the vehicle’s digital components align with user expectations.
3. Remote Diagnostics and Updates*
Digital twins enable remote diagnostics and updates for vehicles. Manufacturers can monitor real-time data from vehicles, identify potential issues, and even provide software updates to enhance performance.
Example: A manufacturer of electric vehicles employs digital twins to simulate the charging behavior of their vehicles. By analyzing charging patterns, battery life, and energy consumption in a virtual environment, they optimize the vehicle’s charging infrastructure and battery management.
Driving Forward with Digital Twins
In conclusion, the automobile industry is embracing digital twins as a catalyst for innovation and efficiency. From design and manufacturing to performance testing and future mobility, these virtual replicas are driving advancements that shape the future of vehicles. By simulating and optimizing every facet of the automotive lifecycle, Digital Twins is propelling the industry toward a future of smarter, safer, and more sustainable mobility solutions.