Revolutionizing Manufacturing: Unleashing the Power of Digital Twins in Factories
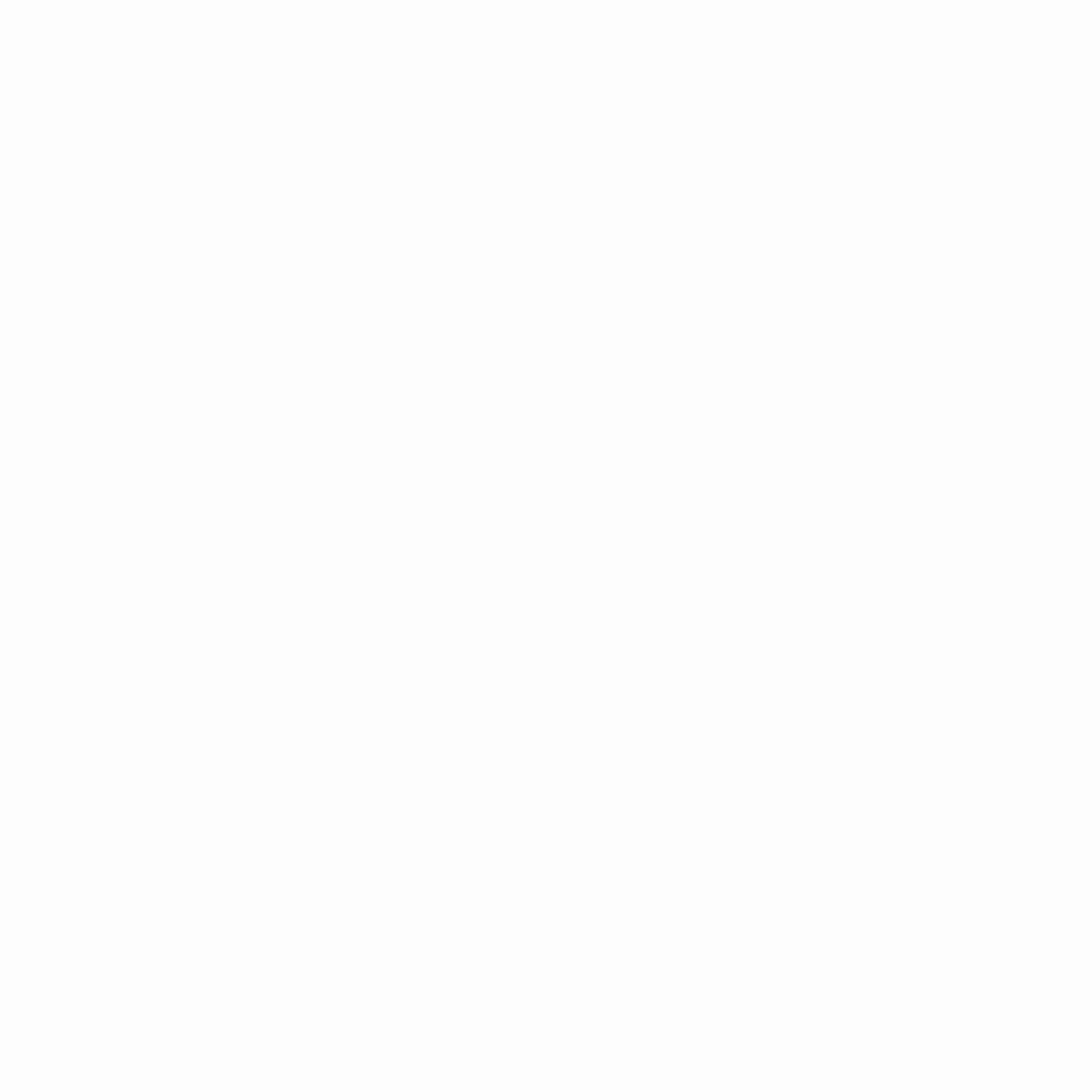
In the realm of modern manufacturing, the integration of digital twins has emerged as a game-changing innovation, reshaping the way factories operate, optimize processes, and achieve unparalleled levels of efficiency. This article explores how Digital Twins can be effectively utilized in factories, accompanied by real-world examples that showcase their transformative potential across various aspects of manufacturing.
1. Product Design and Development
Virtual Prototyping and Testing
Digital twins enable manufacturers to create virtual prototypes of products before physical production begins. This facilitates thorough testing, design refinements, and identifying potential issues early in the process.
Example: An automobile manufacturer can develop a digital twin of a new car model, simulating performance under different conditions, such as acceleration, braking, and impact tests, to ensure optimal safety and functionality.
Iterative Design Optimization
Manufacturers can use Digital Twins to iterate and optimize product designs swiftly. Virtual simulations allow for testing variations in materials, components, and geometries to achieve the best possible outcomes.
Example: A consumer electronics company can use a Digital Twin to experiment with different cooling mechanisms for a new smartphone design, ensuring efficient heat dissipation and prolonged device life.
2. Production and Assembly
Process Simulation and Optimization
Digital twins enable manufacturers to simulate production processes, predicting bottlenecks, optimizing workflows, and reducing downtime through accurate predictions of equipment performance.
Example: In an aerospace factory, a Digital Twin can simulate the assembly line for a new aircraft model, optimizing the sequence of tasks and resource allocation to minimize production time and costs.
Predictive Maintenance
Manufacturers can use digital twins to monitor machinery health and predict maintenance needs. This helps prevent unexpected breakdowns, reduce downtime, and optimize maintenance schedules.
Example: A steel manufacturing plant can use a digital twin to analyze real-time data from sensors on critical equipment, predicting when maintenance is required to prevent costly production stoppages.
3. Quality Control and Inspection
Automated Inspection
Digital twins facilitate automated quality control by comparing physical products to their virtual counterparts. Deviations can be identified quickly, enabling corrective actions and ensuring consistent product quality.
Example: A pharmaceutical company can use a digital twin to compare the dimensions and features of each pill to its virtual representation, ensuring that every dose meets strict quality standards.
4. Training and Skill Development
Training Simulations
Manufacturers can use digital twins to create realistic training simulations for employees. This allows new workers to familiarize themselves with processes and equipment before entering the factory floor.
Example: An electronics manufacturer can develop a digital twin-based training program that simulates complex soldering processes, enabling new technicians to practice their skills in a risk-free environment.
5. Supply Chain Optimization
End-to-End Visibility
Digital twins provide a comprehensive view of the entire supply chain, allowing manufacturers to track the movement of raw materials, components, and finished products in real-time.
Example: An automotive manufacturer can use a digital twin to monitor the location, condition, and expected arrival times of components from various suppliers, ensuring smooth production schedules.
6. Environmental Impact Reduction
Energy Consumption Analysis
Digital twins can analyze energy consumption patterns in factories, identifying opportunities for energy efficiency improvements and helping manufacturers reduce their environmental footprint.
Example: A food processing plant can use a digital twin to analyze the energy consumption of different production lines, optimizing equipment usage and reducing overall energy usage.
7. Continuous Improvement and Innovation
Data-Driven Decision-Making
Digital twins provide manufacturers with data-driven insights to optimize processes continuously. By analyzing historical data, manufacturers can identify trends and areas for improvement.
Example: An industrial chemical plant can use a digital twin to analyze historical data on chemical reactions, identify optimization opportunities, and enhance product yield.
Unlocking Manufacturing Excellence
In conclusion, digital twins are revolutionizing manufacturing by offering a virtual mirror that empowers factories to innovate, optimize, and excel across all stages of production. By integrating these virtual replicas, manufacturers can achieve greater efficiency, enhance product quality, and pioneer a new era of manufacturing excellence.